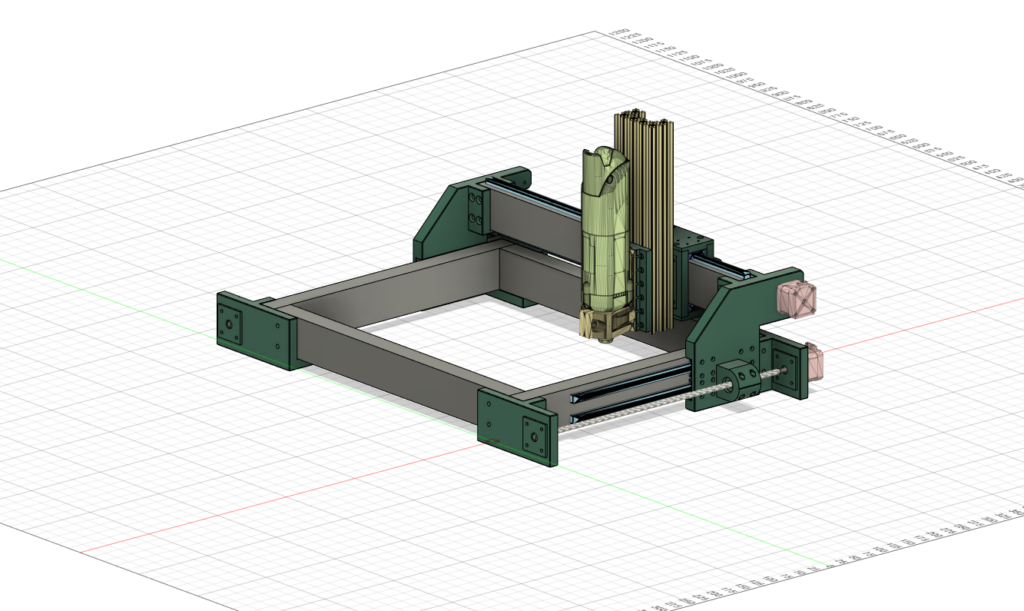
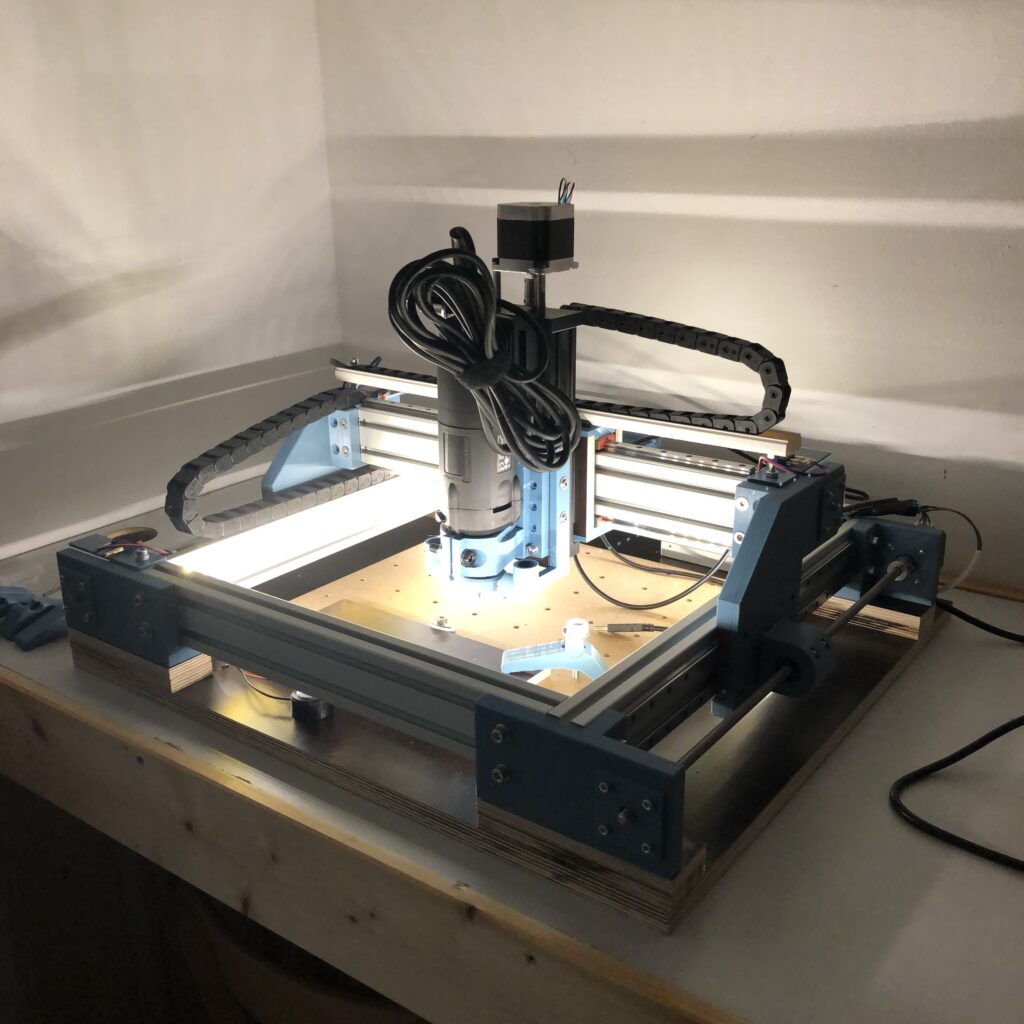
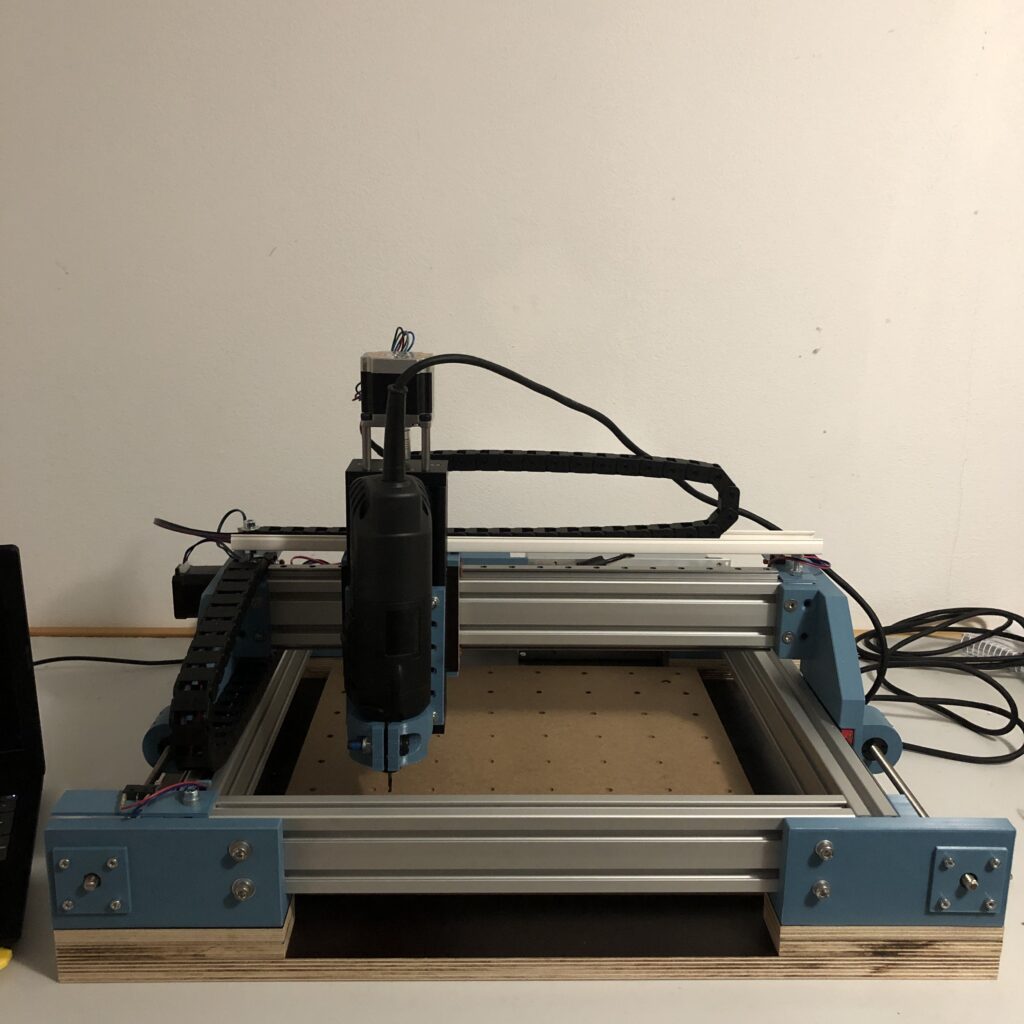
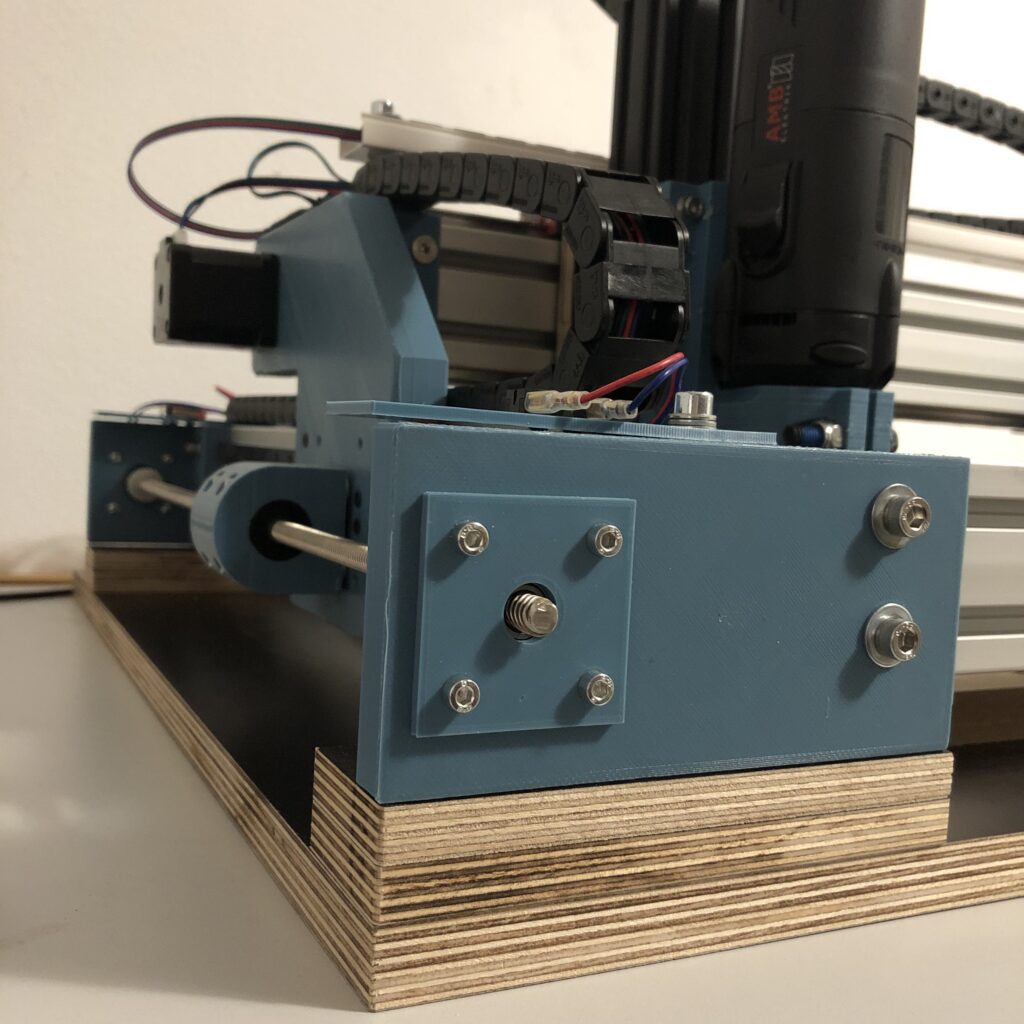
As I began working on my second router, I knew that I wanted to create a machine that was smaller and more streamlined than my first one, without sacrificing any power or precision. I had been pleased with the capabilities of first, but its large size and bulky enclosure were not always practical for all of my projects.
To achieve my goal, I decided to keep the electric side of the project very similar to that of my first router. I used an Arduino Uno paired with a CNC shield as the brain of the machine, and employed a 24 V power supply and Nema 13 stepper motors to move an AMB-ELEKTRIK router mounted on a 600 by 400 millimeter work bed. With a Z-height of 30mm, this router was designed primarily to cut sheet goods.
Throughout the design process, my focus was on creating a machine that was just as powerful as my first router, but more compact and robust. I wanted to be able to transport and operate it in tighter spaces without sacrificing any of its capabilities.